In summary
Today, all post-industrial and post-consumer material waste can be reprocessed through the extrusion process. Waste plastic from industrial production is becoming increasingly valuable in times of rising raw material prices and environmental pollution. We believe that becoming more sustainable is an inevitable path for the plastics industry.
Some of the critical issues that can be encountered during the processing of waste materials can be the high temperatures, pressures involved in the extruder and the stresses involved in the recovery and reprocessing of plastics, creating inevitable degradation processes. These problems severely limit processing and reuse and impact the processability and technical-quality characteristics of the output products.
Another challenge in recycling scrap material can be residual moisture, which is why an extruder during recycling needs venting and degassing systems to remove not only moisture, but also solvents or decomposed materials.
With its system, Bausano aims to solve process problems such as the loss of mechanical properties and the management of increased residual moisture in the selected product, which is a critical parameter that must be managed during processing.
Case History for plastic Recovery of PP & ABS
A single-screw E-GO 45/37 line has just been produced and tested in our testing department. It has been designed for regranulation of industrial post-consumer material, in particular PP and ABS. The customer also requested a further test with glass-fiber reinforced ABS. In this case, the result was influenced by the dispersion and percentage of the filler present in the starting material.
The line was designed with volumetric dosing units for dosing the raw material. The installation of a degasser for stripping the volatile substances formed during melting improved the workability of the material and its technical/qualitative output characteristics. An automatic filter with operating pressure of up to 600 bar, an extrusion head with 16 "spaghetti" holes, a cooling tank, a dryer and a cutter have enabled the re-granulation line to reach a capacity of 200kg/h.
Everything was designed within Bausano, starting with the study of incoming materials and the customer’s specific requests. This demonstrates that our lines are very flexible and can be designed according to the specific productivity and workability needs of the materials proposed.
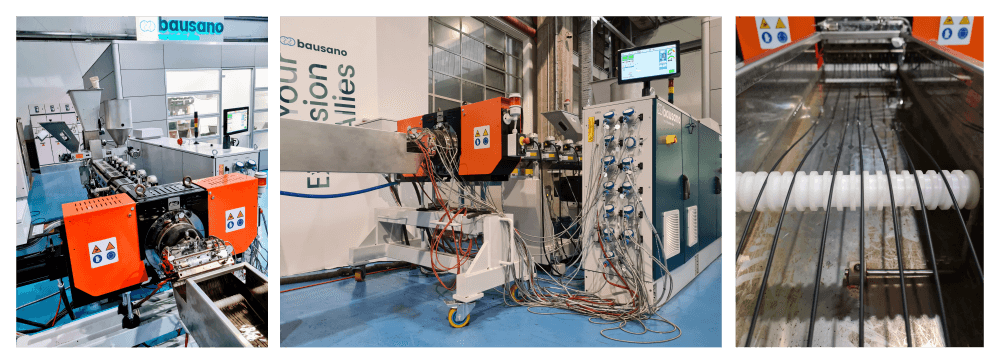
Energy costs represent the third-largest cost item in plastics companies’ budgets and they must be contained to keep the companies highly competitive on the market.
Production machinery, plant lighting and heating systems, and industrial refrigeration systems are just some of the items that contribute to raising the load curve, especially when the company has obsolete and inefficient equipment. The extruder is the most important energy-consuming component of a plastics manufacturing company. A malfunctioning system is not only at risk of failure but also consumes more energy
Designed by our team of engineers, the Barrel Induction Heating System is a Bausano technological innovation that allows savings of up to 35% on extruder consumption.
In the process of induction heating, the metal of the barrel is exposed to an alternating electromagnetic field, generated by a current-carrying coil. These coils consist of special cable wound around a metal core. This non-contact process produces eddy currents in the material, which in turn produce heat.
The main advantages of introducing the Smart Energy System are:
- Ease of installation through the opening coil heater
- Faster heating
- Maximum energy efficiency thanks to electromagnetic induction, which enables the heaters to achieve savings of up to 35%. This is because the thermal energy generated by electromagnetism is not dispersed into the environment but is concentrated within the element to be heated, without the need for any physical contact with the element itself
- Processability of materials at higher temperatures, allowing considerable savings in the processing of those materials that require processing at high temperatures, e.g. PO.
Through constant investment in research and development and continuous technological innovation, Bausano is an ideal partner for the development of a traceable plastics supply chain.
We want to actively participate and transform a currently fragmented production chain (plastics processing chain) into an effective circuit and ensure a quality, efficient and cost-effective final production chain. Our desire is to create a chain of cooperation between those who, like us, are manufacturers of plastic processing machines and those who use our equipment to manufacture products.